Creating a Welding WPS: Step-by-Step Directions for Professionals
Creating a Welding WPS: Step-by-Step Directions for Professionals
Blog Article
Grasping Welding WPS Criteria: Finest Practices and Techniques for High Quality Welds
In the realm of welding, understanding Welding Treatment Requirements (WPS) criteria is an essential element that directly affects the high quality and stability of welds. Sticking to these standards ensures uniformity and dependability in welding results. Nevertheless, attaining excellence in welds exceeds just comprehending the standards; it involves implementing best techniques and strategies that elevate the craft to a degree of accuracy and skill that sets apart the average from the extraordinary. As we browse via the complexities of welding WPS requirements, uncovering key understandings and strategies for attaining top-tier welds will certainly be paramount for welders seeking to succeed in their craft and generate welds that stand the test of time.
Understanding Welding WPS Criteria
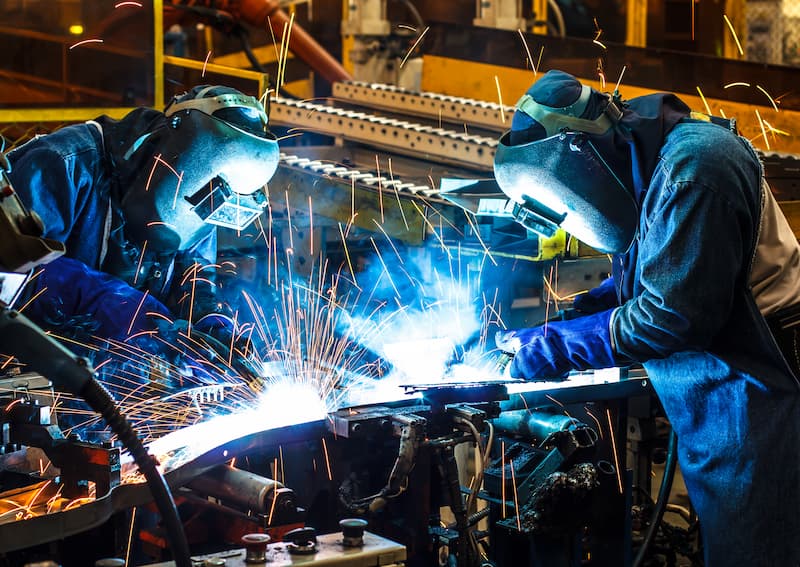
Inspectors rely on WPS documentation to confirm that welding treatments are being complied with appropriately and that the resulting welds are of high top quality. Engineers utilize WPS standards to create welding treatments that guarantee the resilience and integrity of welded structures.
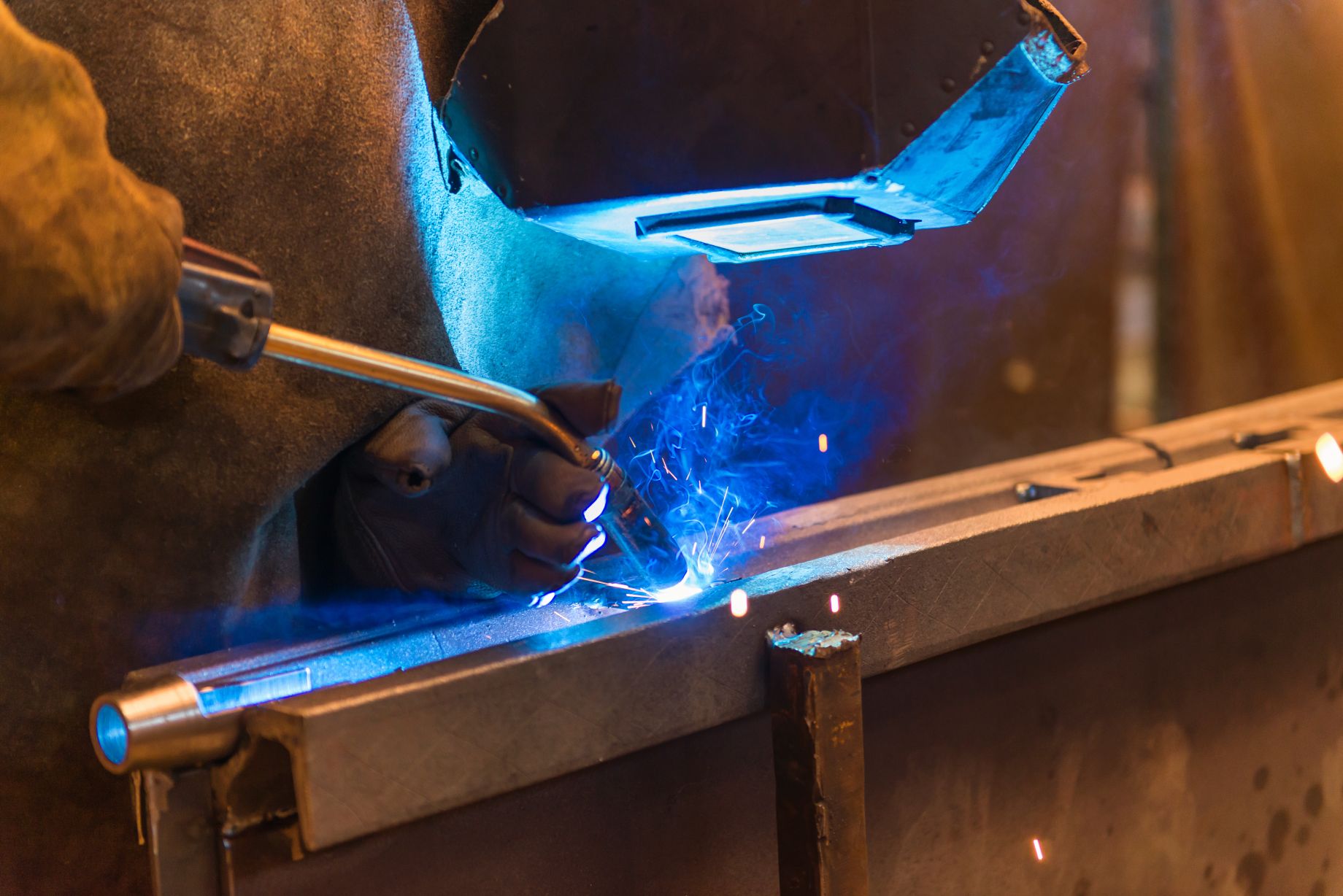

Necessary Tools for High Quality Welds
Grasping welding WPS standards is necessary for welders to successfully utilize the essential devices required for creating top quality welds. The kind of welding device needed depends on the welding procedure being utilized, such as MIG, TIG, or stick welding. Cord brushes and cracking hammers are important for cleaning up the weld joint before and after welding to eliminate any kind of pollutants that can influence the top quality of the weld.
Key Techniques for Welding Success
To achieve welding success, one should grasp the essential methods necessary for producing premium welds. Keeping a steady hand and a stable welding setting throughout the process is key to achieving accuracy and uniformity in the welds. By understanding these crucial methods, welders can elevate the high quality of their job and attain welding success.
Ensuring Conformity With WPS Criteria
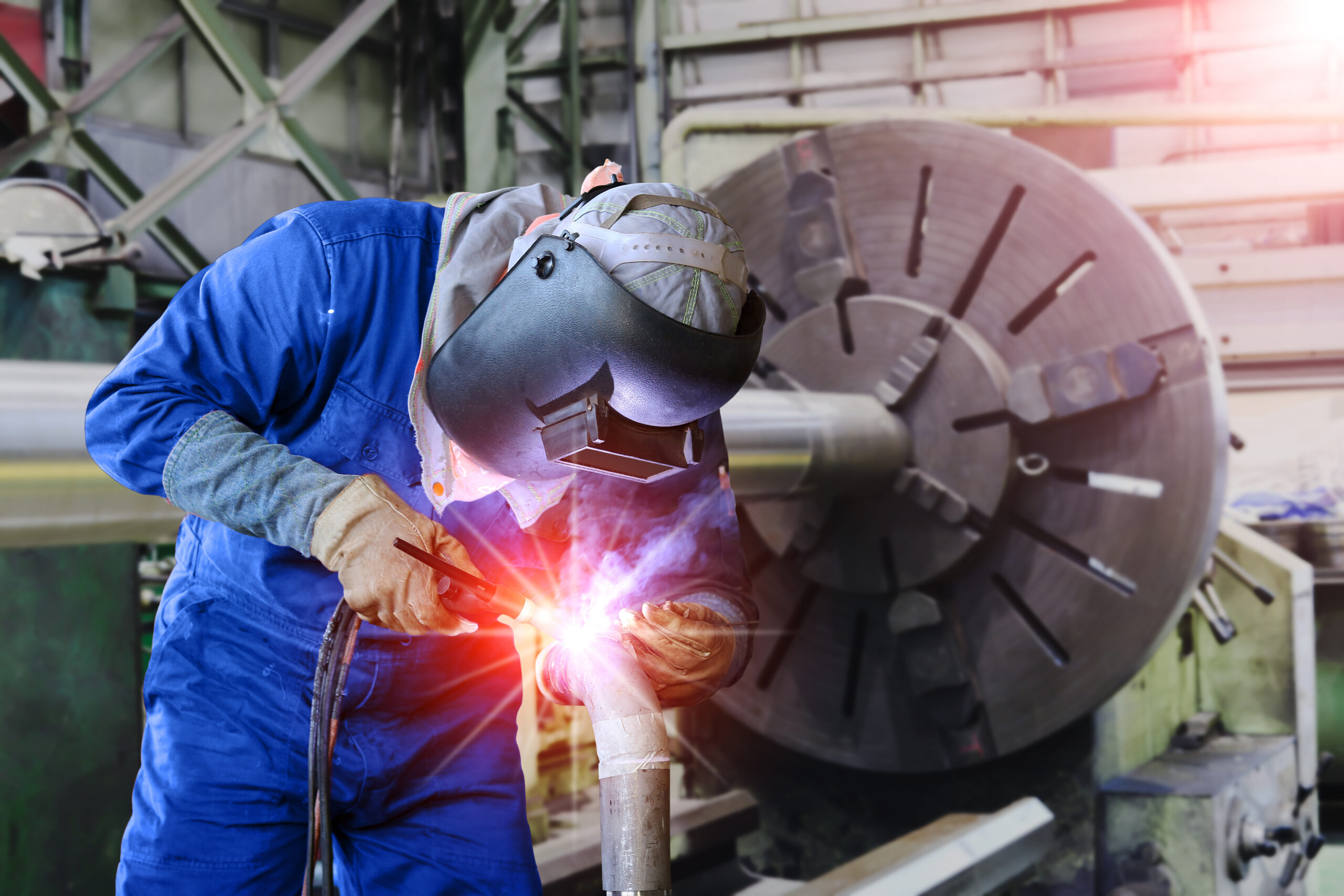
Furthermore, preserving in-depth documents of welding criteria, tools calibration, and inspection results is vital for demonstrating conformity with WPS requirements. By vigilantly sticking to WPS standards, welders can make sure that their work satisfies the necessary quality degrees and contributes to the general success of the welding task.
Troubleshooting Common Welding Issues
When confronted with usual welding issues, identifying the origin is vital for reliable troubleshooting. One prevalent problem is the visibility of porosity in welds, typically triggered by pollutants such as corrosion, wetness, or oil. To resolve this, making sure proper cleaning of the base steel before welding and making use of the appropriate shielding gas can dramatically lower porosity. An additional issue frequently encountered is absence of blend, where the weld stops working to appropriately bond with view it now the base material. This can originate from insufficient warm input or incorrect welding strategy. Changing specifications such as voltage, cable feed rate, or take a trip rate can assist enhance blend. Additionally, distortion, breaking, and spatter prevail welding difficulties that can be alleviated through appropriate joint prep work, constant heat control, and choosing the appropriate welding consumables. By completely comprehending these typical welding concerns and their origin causes, welders can efficiently troubleshoot problems and accomplish top quality welds.
Conclusion
In conclusion, grasping welding WPS standards requires a thorough understanding of the standards, making use of essential tools, and applying crucial techniques for successful welds. Making certain compliance with WPS standards is critical for producing quality welds and preventing typical welding concerns. By complying with ideal strategies and practices, welders can attain reliable and constant results in their welding jobs.
In the world of welding, understanding Welding Treatment Specification (WPS) standards is an essential part that directly affects the high quality and honesty Continued of welds.When diving right into the realm of welding practices, an important facet to comprehend is the significance and details of Welding Treatment Requirements (WPS) requirements. WPS requirements offer an in-depth standard for welding procedures, making certain uniformity, high quality, and safety and security in the welding process. The kind of welding maker required depends on the welding process being utilized, such as MIG, TIG, or stick welding.Achieving welding success with the mastery of essential techniques you can check here demands an extensive understanding and adherence to Welding Procedure Specification (WPS) standards.
Report this page